In an electric vehicle (EV) the lithium-ion battery represents 30 – 40% of the cost. In the battery the battery cells represent 60 – 70% of the cost. Consequently, about 15 – 30% of the cost of an EV are the battery cells.
As important as the cost of the battery cells are the performance characteristics: energy density that translates into range, charging time, safety, life, etc. Altogether, it makes the choice of battery cells crucial for success or failure of an EV.
No company has understood this better than Tesla. They early teamed up with Panasonic, a relation which remains strong today. It is Panasonic, who built, owns and operates the battery cell manufacturing inside Tesla’s first gigafactory. Panasonic started with the 18650 wound cells. Later they changed to the larger 2170 cells. To support Tesla’s growth Panasonic is building a new gigafactory in De Soto, KS, with a planned capacity of 30 GWh and production starting in March this year (2025). Tesla and Panasonic have also worked together developing the 4680 cells. When Tesla in 2019 built its gigafactory in Shanghai they started sourcing battery cells from the leading Chinese companies, CATL and BYD. It reduced costs and increased the margins on the Tesla EVs built there
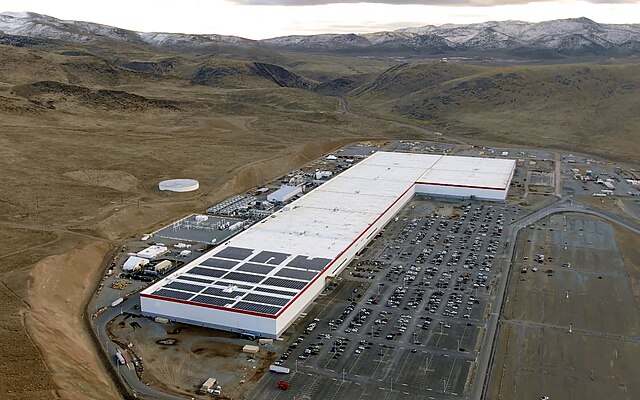
Creative Commons Attribution. Share Alike 4.0
The relations between Tesla and CATL and BYD, respectively have strengthened. Now, CATL is the main provider to Tesla’s bulk energy storage system (BESS) business, both in China and in the US. In Shanghai Tesla is building a dedicated factory for the Megapacks, the building block of utility scale BESS, with CATL building a dedicated battery cell factory there as well. In the U.S. Tesla and CATL takes the same approach, with dedicated factories, but with the difference that Tesla will own and operate the battery cell factory using the manufacturing equipment from CATL, who will assist in setting up and commissioning the production lines. The details of the agreement between Tesla and CATL have not been disclosed. Last year (2024) Elon Musk announced that Tesla will use BYD second generation blade battery for the Model Y cars built in its Berlin, Germany, gigafactory.
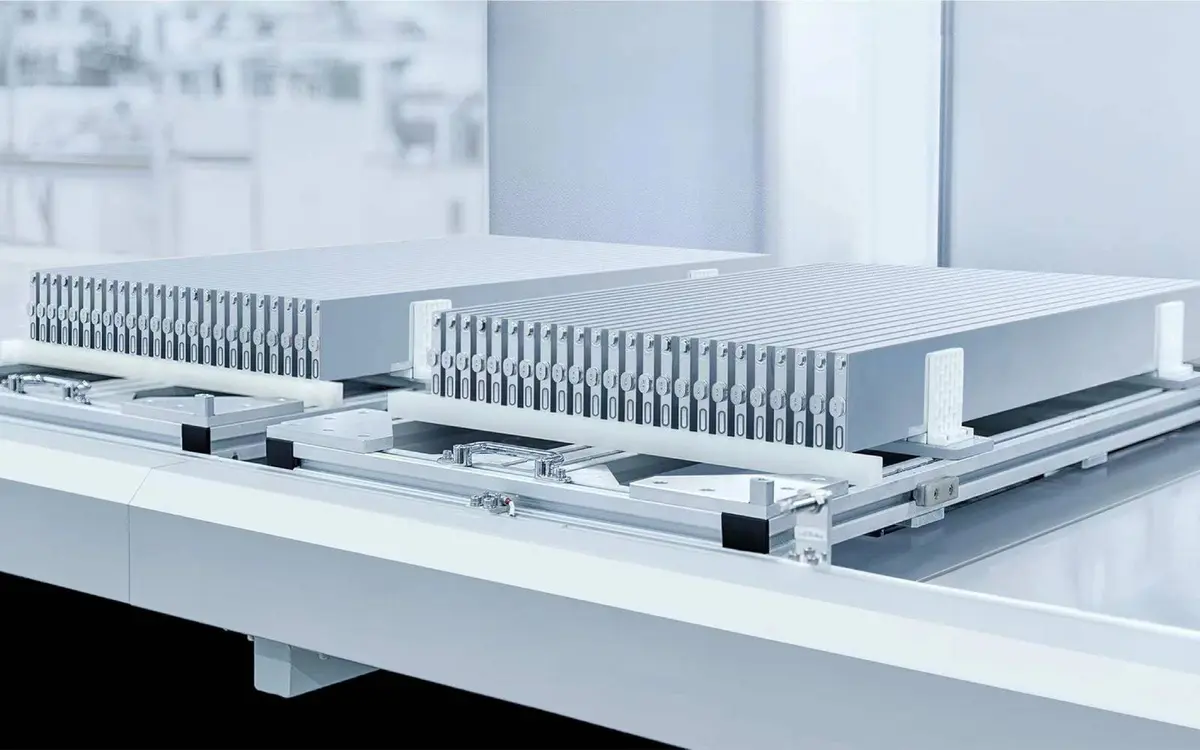
Creative Commons BY4.0 Attribution 4.0 International.
Almost all lithium-ion battery cells in the world are manufactured by Asian companies. According to Statista, for the first half of 2024 CATL had 37.8% market share of EV battery cells, followed by BYD at 15.8% and LG Energy Solutions (South Korea) at 12.9%. Together, these three companies cover two-thirds of the market. CATL and BYD combined over 50% market share. Of the Top Ten companies six are Chinese, three South Korean (LG Energy Solutions, SK On and Samsung SDI) and one is Japanese (Panasonic). Another company of interest is AESC, which was founded as a venture between Nissan and NEC (AESC was founded in 2007 by Nissan and NEC. Since 2019 Envision of China has become the majority owner.
The distinct leadership position of CATL and BYD is thanks to their early (some 15-20 years ago) bets on lithium iron phosphate (LFP) as the cathode chemistry and decades of continuous improvements, economy of scale (China is by far the biggest EV market) and a fierce competitive domestic market. The early investment in LFP was not assured. The nickel-based chemistries NCM (nickel cobalt manganese) and NCA (nickel cobalt aluminum), were preferred by Tesla and the other EV makers thanks to its higher energy density, which translates to better range. Going forward, thanks to remarkable improvements, all indications are that battery cells with LFP cathodes will be the dominant battery cell technology for lithium-ion batteries with CATL and BYD in the lead, but, no doubt, the other companies will follow.
However, the Chinese growing dominance in EVs and lithium-ion batteries have triggered geopolitical concerns both in the U.S. and in Europe. The concerns turned into explicit actions last year (2024). The import tariffs for EVs from China have been raised to 100% in the US and to 35% in addition to the existing 10% duty in Europe. For batteries and battery cells the tariffs have been raised to 25% both in the U.S. and Europe. It went into effect in 2024 for vehicle applications. For stationary battery storage applications in the US, it is scheduled to be implemented in 2026.
The response by the Asian companies has been to build battery cell factories in the US and in Europe. In the US, the Government has encouraged this development, which accelerated through the Inflation Reaction Act (IRA). However, Chinese companies are excluded from the IRA generous support. Still, Chinese companies like EVE Energy and Gotion HiTec are building manufacturing capacity in the U.S. Almost two-thirds of the new battery cell capacity is being built South Korean companies like LG Energy Solutions, which since 2012 has a factory in Holland, MI. It is being expanded to 25 GWh this year (2025). LG Energy Solutions also formed a joint venture, Ultium Cells LLC, with General Motors (GM). CATL, concerned about further restrictions, has refrained from building its own factories in the US. Instead CATL has chosen a route of partnerships and licensing programs. With Tesla it is already in place, but when Ford and GM try to take the same approach, lawmakers have raised concerns. Complicating matters further was the “blacklisting” of Department of Defense (DOD) in January this year (2025) designating CATL as a “Chinese Military Company”, something CATL has strongly objected.
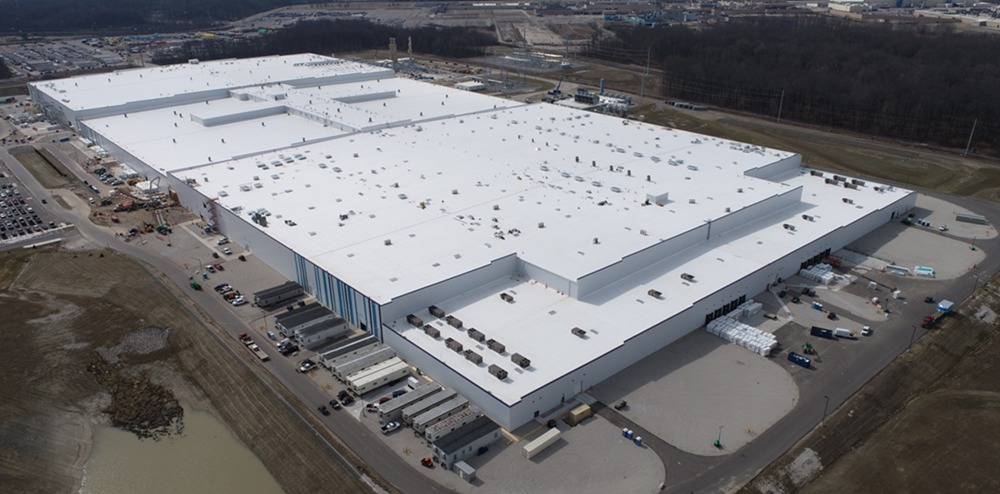
Picture from Ultium Cell’s website.
Europe has taken a more measured approach, open for Asian companies, including the Chinese, to set up factories in Europe. Nevertheless, concerned about the Chinese growing strength in EVs and batteries, the European Commission announced in 2017 the creation of the European Battery Alliance aiming for a “strong independent European battery industry” with support from the European Investment Bank (EIB). Northvolt became the flagship company for this wish/effort. Trying to do this from scratch and without any previous knowledge or unique technology turned out to be overwhelming. Northvolt filed for Chapter 11 in November 2024 after producing less than 1% of Northvolt 1 (Sweden) factory’s 16 GWh capacity and spending around $6 billion. At that time, the company had only $30M in cash, but $5.8 B in debt. Northvolt’s failure seems to have accelerated the efforts of CATL and BYD, and other Chinese companies to strengthen their presence in Europe. CATL has already factories in Germany and Hungary. In December last year (2024) CATL and Stellantis announced a joint venture to set up a battery cell factory in Spain with production to start by the end of 2026 with a capacity up to 50 GWh. Also, the South Korean companies are expanding existing factories or building new ones. In fact, LG Energy Solutions was the first battery company to set up a factory in Europe already 2016. This factory, located in Wroclaw, Poland, is now by far the largest battery cell factory in Europe with a capacity of 86 GWh.
Building regional supply chains in North America and Europe will take time, but it should eventually reduce geopolitical concerns. The transition from nickel-based battery cells, including NCA and NCM, to LFP-based battery cells should also more effectively enhance the development of regional supply chains. After all, iron and phosphate are much easier to find locally than it is to source nickel, cobalt, and manganese!
Tariffs on EVs may delay the growth of Chinese EVs in North America and Europe, but for North American and European EV car companies to have a fighting chance to be competitive they have no choice but, in addition to the South Korean and Japanese companies, to also source battery cells from the Chinese battery companies either directly or through partnerships or through licensing.